High-Precision Small Part CNC Machining: Achieve Unmatched Accuracy
The World of Small Part CNC Machining: Precision at a Miniature Scale:
Small part CNC machining is the gold standard in the manufacturing industry, where even a millimeter can have a huge impact. Utilizing computer numerical control (CNC) technology, this highly specialized technique produces complex and accurate components, with dimensions frequently expressed in fractions of a millimeter.
When it comes to making high-tolerance parts for medical devices or intricate gears for miniature robotics, this CNC machining provides unmatched precision and reproducibility. This article explores the advantages, uses, and success factors of CNC machining, delving into this intriguing field.
Unveiling the Advantages of Small Part CNC Machining:
Many businesses use small-component CNC machining because it has numerous benefits over conventional machining techniques. These sectors include:
- Unmatched Precision:
CNC machines produce products with remarkable dimensional accuracy and tight tolerances by using computer-controlled cutting tools. This is important for applications where functional compromise can occur from small variances.
- Complexities Made Easy:
Difficult designs and complex geometries are no match for small part CNC machining. You may get remarkably precise round features, crisp corners, and small details.
- Repeatability on Demand:
One of the great things about CNC programming is its capacity for perfect part replication. Every component made complies with the precise requirements, guaranteeing quality and consistency throughout a production run.
- Material Versatility:
CNC technology may be used to efficiently process a wide range of materials, from strong metals like titanium and stainless steel to delicate polymers. This makes it possible to create parts that are appropriate for a variety of uses.
Quick prototyping:
In the process of developing new products, the capacity to create prototypes fast is crucial. Before concepts are put into mass production, designers and engineers may test and refine them more easily thanks to a small part CNC machining.
Cost-Effectiveness for Small Batches:
CNC machining excels in producing small batches quickly and cheaply, in contrast to traditional machining technologies that demand a large setup time and tooling expenses. Because of this, it’s an affordable option for projects that just need a few parts.
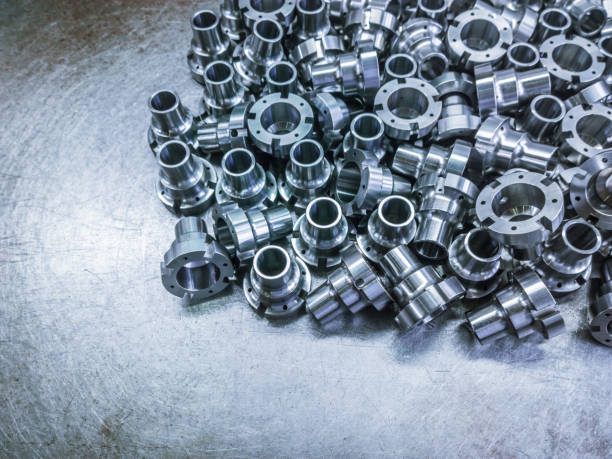
Applications: Where Small Parts Make a Big Impact?
Beyond the examples given, tiny part CNC machining has far-reaching effects. Here’s a closer look at a few other sectors that depend on this exact production method:
- Automobile:
This CNC machining is essential in the automotive sector, where it is used for anything from lightweight parts for increased fuel economy to complex engine components and fuel injectors. The smooth operation and long-term durability of these vital components are guaranteed by strict tolerances and high-performance materials.
- Consumer Electronics:
This CNC machining is the driving force behind the shrinking of laptops, smartphones, and other consumer electronics. Thanks to this technology, devices can now be made that are both powerful and small, with intricate features housed in a smaller package.
- Telecommunications:
They play a key role in the telecommunications sector, from complex components in cell phone towers to tiny connectors in fiber optic cables. Efficient data transmission and unambiguous communication are contingent upon precision and dependability.
- Weapons:
High-precision tiny parts play a major role in the complex mechanisms of weapons. The safe and trustworthy operation of weapons is ensured by the manufacture of robust and dependable parts like triggers, sears, and ejectors made possible by CNC machining.
- Optics:
Small part CNC machining is frequently used in the production of optical lenses, mounts, and other delicate parts found in microscopes, telescopes, and other optical equipment. For optical applications to function at their best, remarkable surface qualities and close tolerances are essential.
This CNC machining continues to transform many industries and push the frontiers of design and innovation by making it possible to create these tiny marvels. Check out our in-depth guide on our website for a closer look into the realm of CNC machining for particular industries.
Demystifying the Process: Techniques for Small Part CNC Machining:
For bigger parts, a variety of CNC machining techniques can be used; however, specialized methods are needed to achieve accuracy and efficiency with tiny components. A closer look at the top three methods for small part CNC machining are as follows:
- Micro Milling:
Using tiny cutting tools with dimensions as small as 0.002 inches (0.05 mm), micro milling is a specialized type of CNC milling. These tools can create sharp angles and detailed details on very small workpieces because of their fast speed of operation. High spindle speeds (the tool’s rotating speed), which can approach 100,000 RPM on micro milling machines, allow for precision material removal for intricate designs.
- Swiss Machining:
It is also known as Swiss Screw Machining: This special method works well for creating long, thin pieces with detailed details. The machine constantly feeds a bar-fed stock material through which numerous tools are positioned around a rotating bar to execute different machining operations at the same time. Swiss machining is incredibly accurate and efficient, especially when it comes to pieces with small diameters and intricate shapes. Because the material is fed continuously, there is less material waste generated, which makes it an affordable choice for large-scale production of small parts.
Optimizing for Success: Design Considerations for Small Part CNC Machining:
As precise as a tiny part of CNC machining might be, planning with manufacturability in mind is essential to getting the best possible outcomes, keeping costs down, and guaranteeing effective production. The following are important design factors to remember:
- Wall Thickness:
Walls with a thickness of less than 0.5 mm can be difficult to mill and are more likely to break. Strive for a balance between preserving enough wall thickness for structural integrity and decreasing the amount of material used. Early in the design process, speaking with your CNC machining partner can help you figure out what the perfect wall thickness is for your particular application.
- Sharp Corners and Tight Radii:
Although CNC machining can produce sharp features, there are several advantages to introducing slightly bigger radii (curved edges) into corners. Greater radii increase tool clearance, which lowers the possibility of tool breakage and boosts machining effectiveness. They can also reduce the part’s stress concentrations, which is beneficial for components that are carrying heavy loads.
- Deep Pockets and Undercuts:
Deep pockets and undercuts, or regions unreachable from the top, can be difficult for machining tools to operate in. It is best to redesign parts to reduce these features if possible. As an alternative, think about adding details to the walls of deep pockets, such as draft angles (slight tapers), to make it easier to remove material and access tools. Talking with your CNC machining partner about alternate manufacturing techniques like EDM (Electrical Discharge Machining) may be required if undercuts are required.
The Material Selection:
The success of tiny part CNC machining can be greatly impacted by the material selection. When choosing a material, take into account aspects like cost, weight, machinability, and strength. For example, some materials, such as specific high-strength alloys, may be more difficult to process and need specific tooling, which could result in higher prices. To guarantee a seamless and economical manufacturing process, discuss material selection with your CNC machining partner.
You may optimize your small parts for effective and profitable manufacturing by adhering to these design principles and working closely with your CNC machining partner. This will open the door for high-quality, useful components that satisfy your particular requirements.
5-Axis CNC Machining: The Powerhouse for Tight Tolerance Small Parts:
5-axis CNC machining is the best method for obtaining fine precision and complex geometries in small items. By adding two more rotational axes (A and B), this cutting-edge technology expands on the possibilities of conventional 3-axis machining (X, Y, and Z). Because of this, the cutting tool can approach the workpiece from almost any angle. It opening up a whole new range of possibilities for intricate patterns with precise tolerances.
- Even the most complex details can be machined with extreme accuracy. Because of the machine’s ability to move around the workpiece in several axes. This is necessary to achieve the tight tolerances required for small component performance and operation.
- Complex products can frequently be finished in a single setup when using 5-axis machining. This reduces the possibility of error and boosts production productivity by doing away. The necessity for several setups that come with standard 3-axis machining.
- 5-axis machining easily handles difficult geometry. Extremely precise machining of curved surfaces, undercuts, and sharp angles enables the production of incredibly complex and useful tiny parts.
Conclusion:
In the realm of intricate designs and demanding applications, a small part of CNC machining stands as a testament to human ingenuity and technological prowess. Here at HuaYu prototype, we harness the power of CNC technology to bring your miniature visions to life. Whether you require high-precision components for medical devices, aerospace parts with exceptional tolerances. The rapid prototyping for innovative product development, our expertise in small part CNC machining delivers unmatched results.